In the design and manufacturing world, turning a brilliant idea into a tangible reality requires a robust process known as fabrication. The fabrication involves transforming raw materials into finished products, allowing creators to bring their concepts to life. Whether creating intricate sculptures, constructing buildings, or crafting innovative machinery, fabrication is crucial in various industries.
In this article, we will explore the fascinating journey of fabrication, from the initial concept to the final product, and uncover its immense power.
Pre-Fabrication Phase
Initially, the fabrication process begins with an idea, a concept that ignites the spark of creativity. This pre-fabrication phase involves brainstorming, researching, and formulating a comprehensive plan. In general, engineers, designers, and artists collaborate to refine the concept, considering functionality, aesthetics, and practicality.
Once the concept is solid, detailed designs and blueprints are designed. These drawings provide a roadmap for the fabrication process, guiding the artisans and technicians throughout the journey.
Fabrication Techniques and Processes
With the blueprints in hand, the fabrication process moves into full swing. Various techniques and methods are employed, depending on the nature of the project and the materials involved.
- Cutting and Shaping: This fundamental step involves cutting raw materials into the desired shapes and sizes. Techniques such as laser, water jet, die, and plasma cutting offer precision and efficiency, ensuring accurate results.
- Joining and Welding: Joining different components is a critical aspect of fabrication. Welding, brazing, soldering, and adhesive bonding are standard methods to create solid and seamless connections.
- Forming and Bending: Forming and bending processes are utilized to achieve specific shapes and curves. Techniques like roll forming, press brake bending, and hydroforming mold materials as required.
- Casting and Molding: For projects requiring replicating the same object, casting and molding techniques are employed. These processes involve creating molds and pouring molten material into them, resulting in identical replicas.
Tools and Equipment
The fabrication process relies heavily on diverse tools and equipment, each designed to perform specific tasks with precision and efficiency. CNC machines (Computer Numerical Control), welding machines, press brakes, and lathes are just a few examples of advanced equipment used in modern fabrication facilities.
Quality Control and Precision
In the world of fabrication, precision is paramount. Even the slightest deviation from the intended specifications can significantly affect the final product’s performance and aesthetics. Therefore, quality control measures are implemented throughout the fabrication process to ensure that every component meets the highest standards of accuracy and functionality.
Inspectors and technicians carefully monitor each step, conducting tests, measurements, and inspections to detect imperfections. Manufacturers can deliver products that meet or exceed customer expectations by maintaining strict quality control.
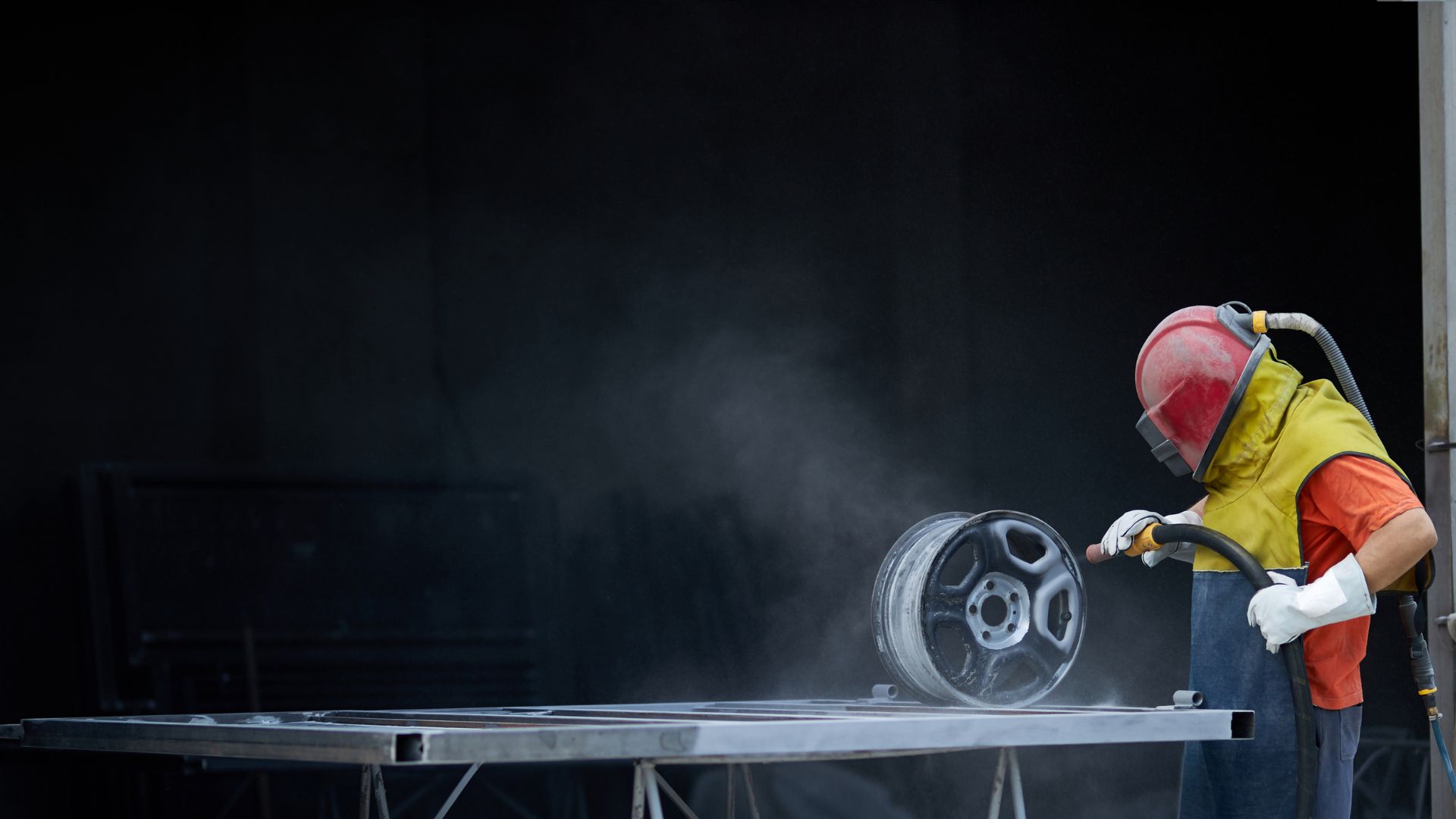
Finishing and Surface Treatments
Once the fabrication process is complete, attention turns to the finishing touches. Surface treatments are applied to enhance the product’s appearance, durability, and performance. For example, surface preparation techniques, such as sandblasting and chemical cleaning, ensure the materials are ready for coatings or finishes.
Painting, powder coating, anodizing, and plating are standard finishing methods to protect the material from corrosion, add color and texture, and improve overall aesthetics.
Case Studies: Real-Life Examples
To truly understand the power of the fabrication process, let’s delve into some real-life examples where this remarkable technique has been harnessed to create awe-inspiring projects.
- The Eiffel Tower: An iconic symbol of engineering and design, the Eiffel Tower was constructed through an elaborate fabrication process. The precision of the metal components and the intricate assembly required meticulous planning and execution.
- Sculptures by Alexander Calder: Calder’s renowned mobiles and large-scale sculptures are created through cutting, bending, and welding. These intricate artworks showcase the limitless possibilities of fabrication in art.
Future Trends in Fabrication
As technology advances, the fabrication process continues to evolve. Emerging technologies like 3D printing, robotics, and automation are revolutionizing the industry, allowing even more intricate designs and streamlined production processes. The future holds exciting possibilities for the fabrication world, paving the way for innovative creations that were once unimaginable.
Conclusion
All in all, the fabrication process is a remarkable journey that transforms ideas into reality. From concept to reality, this process requires careful planning, skilled craftsmanship, and an unwavering commitment to precision and quality. The raw material is formed, joined, and transformed with each step, culminating in a finished product that reflects its creators’ creativity, vision, and expertise – finally ready for product launch. Through fabrication, the impossible becomes possible, and dreams take tangible form.